Maintainance Services
The purpose of this method of statement is to describe the measures and ways of proper application of waterproofing membrane in our project. Work shall be carried out as per the drawing and project speciation.
Work Procedure
Any undulation or protrusions on the surface would be removed in order to obtain smooth surface. The surface must be thoroughly cleaned and free from dust, dirt, loose materials, oils or grease.
50x50mm size fillet made of cement-sand (1:3) mix would be placed along corners of walls or neck columns and any other junctions.
Application
For horizontal waterproofing membrane application. ONE/TWO layer of 4mm thick modified bituminous membrane shall be laid fully torched on binding concrete with minimum of 100mm end laps and 150mm side laps
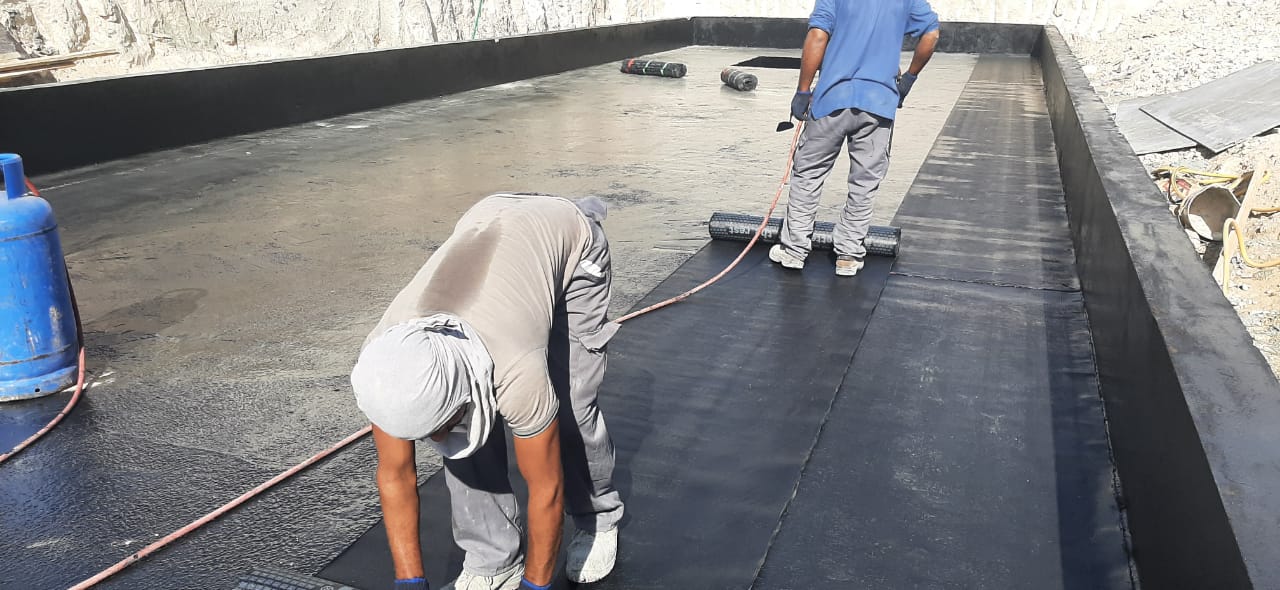
- The binding surface shall be primed with the primer recommended by manufacturer of the membrane prior to placing the membrane. Prior to succeeding works the applied primer shall be inspected by engineer 24hours after the placement.
- Waterproofing membrane installation shall be performed using cylinder fed propone gas torch, trowel to seal the seams of the membrane and knife cutting.
- The membrane is then un-rolled again and torched on pressing the melted area against the substrate. The membrane is then placed in the correct torching position then re-rolled for about half of its length without changing it orientation
APPLICATION OF WATERPROOFING MEMBRANE
- An extra length of minimum 300mm of the horizontal membrane shall be left to carry up the vertical surface to maintain continuity of the membrane and be protected as above.
- For VERTICAL application, two layers of 4mm thick modified bituminous waterproofing membrane shall be applied to all vertical surfaces of grunted shoring or blockworks wall.
- The extra portion of 300mm of the horizontal membrane left shall be turned up and wrapped on to the vertical primed surfaces. The continuity of the membrane shall be maintained by minimum laps 150mm Before applying the waterproofing membrane, concrete surface shall be primed with primer recommended by manufacturer of the membrane but again it should be inspected by engineers 24 hours after the placement.
- The membrane on the exposed external vertical surface shall be carried up to a minimum of 150mm above the finished ground level (.i.e. side wall, parapet etc.) and tucked into a continuous groove provided for the same ad secured firmly with approved sealant/ mastic recommended by the manufacturer of the membrane.
- The membrane fixed on the grunted or concrete wall shall be protected from any damage due to rebar fixing, formworks, concreting of raft, retaining wall works with approved type protection board fixed to the membrane.
- All areas of the membrane exposed above ground shall be protected with appropriate flashing.
- Inspection would be submitted for approval of engineers. Before fixing the steel reinforcement for foundation, the membrane shall be covered by one layer of geotextile and poured with 50mm thick layer of cement sand screed.
Floor Coating & Traffic Guard
Epoxy coatings are durable coatings that can be used for a variety of purposes from strong adhesives to durable paint and coatings for floors and metals. Epoxy coatings are created through the generation of a chemical reaction using an epoxide resin and a polyamine hardener. When these two chemicals are combined, a process called “curing” results. This process can take anywhere from several minutes to several hours and turns the liquid epoxy coating in to an extremely strong and durable solid simultaneously.
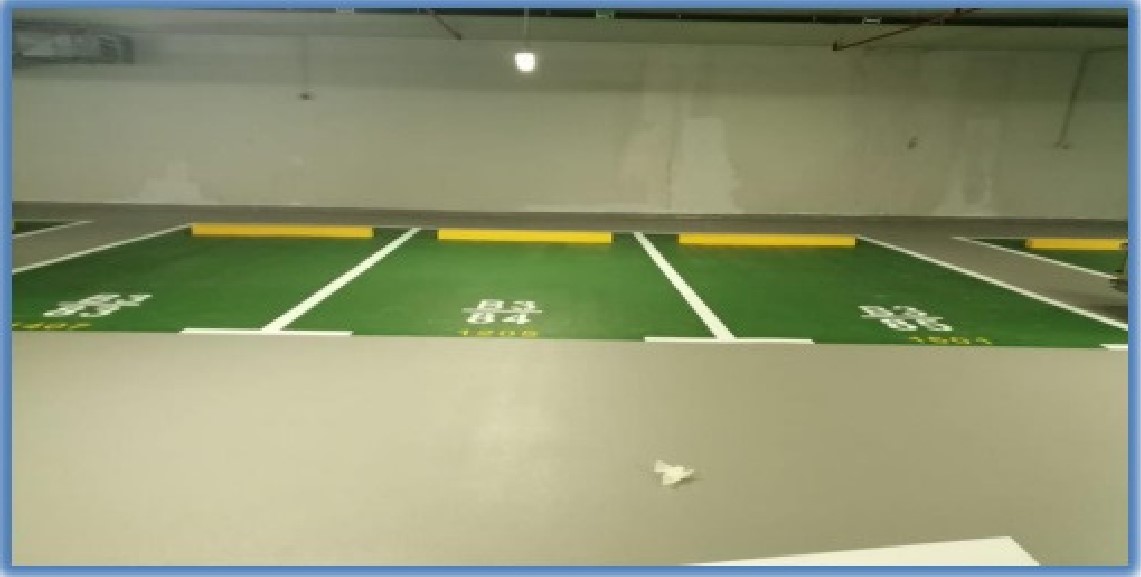
Because of its ability to create a strong, durable, and chemically resistant substance, epoxy and epoxy coating compounds can be used for a variety of purposes.
You can find epoxy coatings used throughout industrial manufacturing plants, in composite materials such as carbon fiber and fiberglass, and in a variety of electrical, automotive, and marine applications. Epoxy materials and epoxy coating compounds can also be used as durable adhesives in a variety of applications.