Combo Waterproofing System
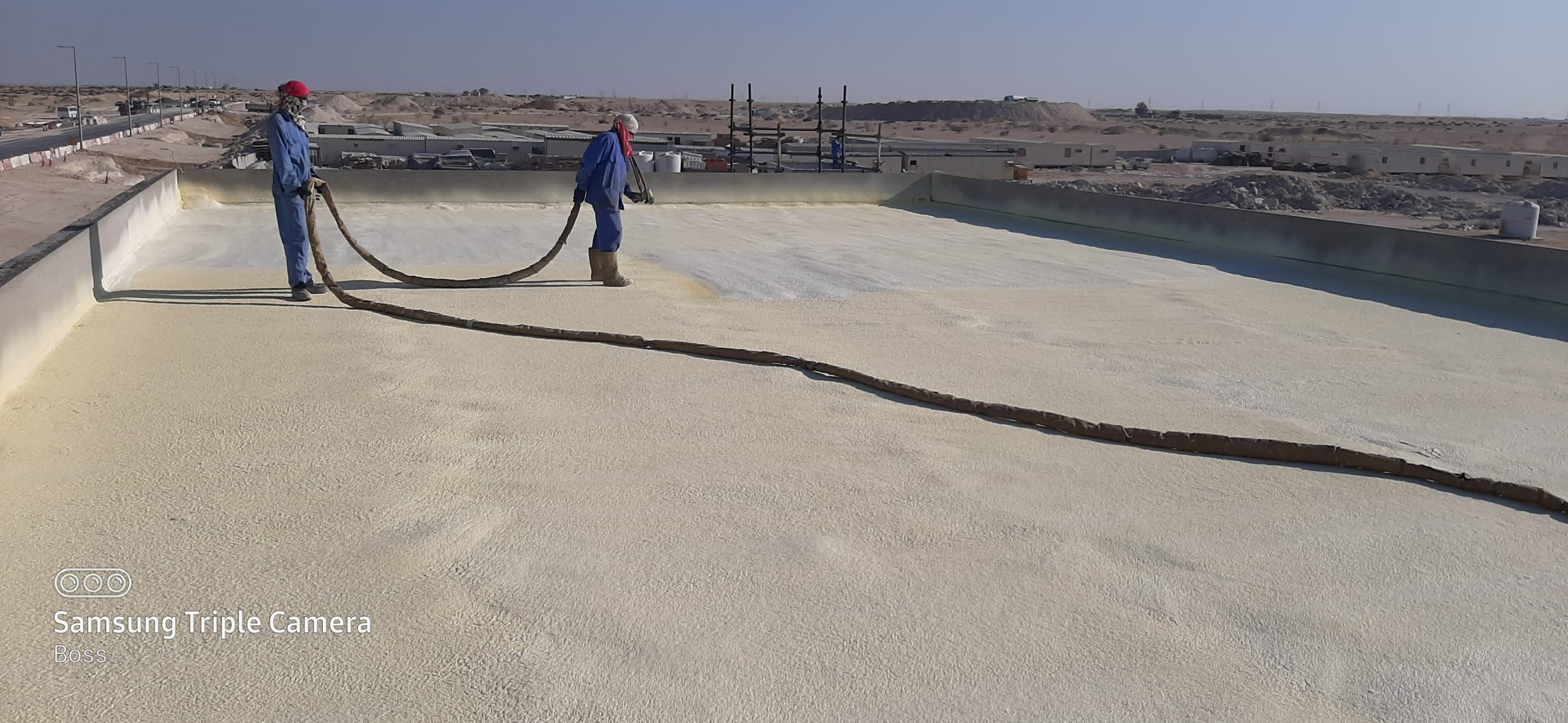
- Prior to the application of the polyurethane foam, ROOF SECURE will check first After the environmental and substrate conditions has been checked and found within the limit, the spraying activity will commence.
- The two (2) components of the polyurethane material Polyol and Iso PMDI will be mixed at 1:1 by volume as per the manufacturer’s instruction through the aid of the specified spray machine. Using the spray foam machine spray the mixture of PUR foam Polyol and PMDI on the prepared substrate. The spraying will be done in horizontal or vertical directions in layers prior to achieving a thickness.
- The spray polyurethane foam will be extended at the vertical areas and to be terminated at a maximum height of 15.0 cm. The environmental and substrate conditions such as wind speed (< 30 Kph), relative humidity (< 80 %), concrete or slab surface moisture content (< 20 %) as per manufacturer’s recommendation.
RUBBERIZED BITUMEN EMULSION (RBE)
The spray polyurethane foam will be extended at the vertical areas After reaching the required thickness of the thermal insulation, and to be terminated at a maximum height of 15.0 cm.
Immediately, using brush or roller, apply the first coat of single component acrylic based high flexible elastomeric water-proof coating RBE to the entire surface of the polyurethane foam. RBE will be allowed to dry for 8 hours minimum (depending on site condition) prior to hours (maximum) water test.
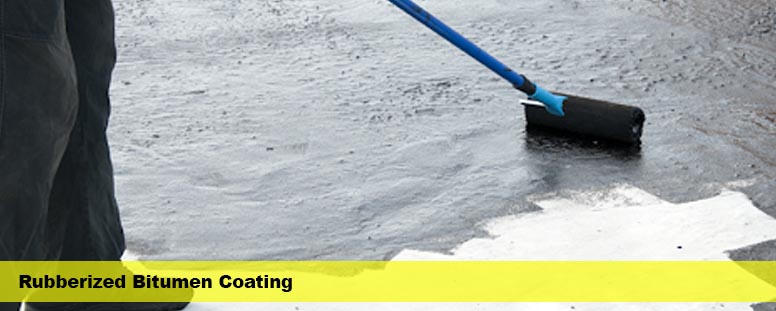
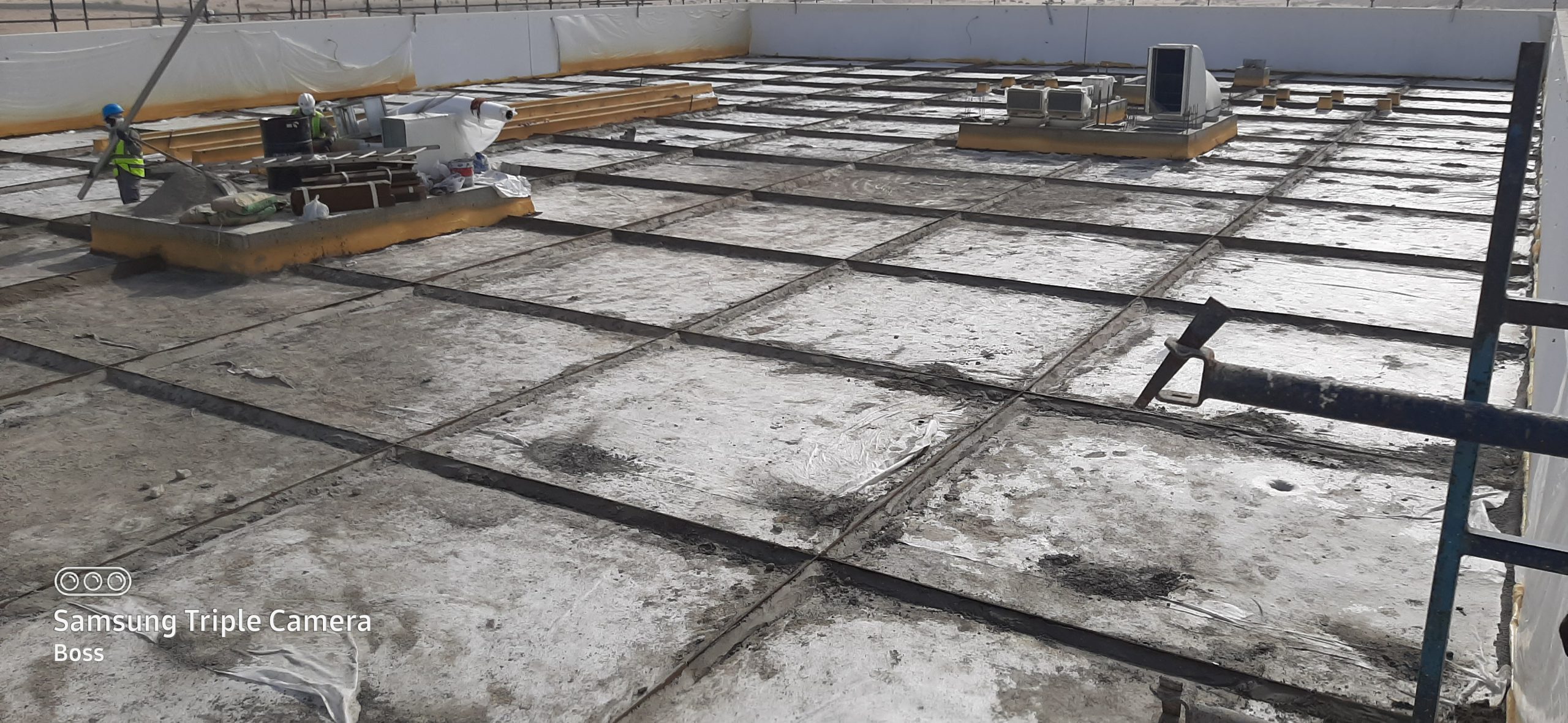
- After successful test, water will be remove and a 1 – layer geotextile will be loosely laid at an overlap of 20 – 30 cm. The geotextile will be extended up to the vertical surface of the previously applied system.
- Upon completion of the geotextile, the roof will be compartmented to rectangular or square shape at 6 m2 maximum using 12 mm thick Flexcell board. These boards will guide the slope as shown in the drawings. The boards will be fixed in accordance to the approved highest and lowest levels as shown in the approved slope shop drawings. The Flexcell Board will be fixed above the geotextile by sand cement mortar to keep it in vertical position.
- After the completion of the compartmentalization, a concrete screed (ready mix) will be casted. Casting of the concrete screed will be made thru the available concrete pumps or equivalent in the site. Level of the concrete screed will follow slope of the previously installed flexcell board. The screed will be smoothly finished (power floated) and will be cured for 2 days minimum.
READY MIX SCREED IS IN PROGRESS
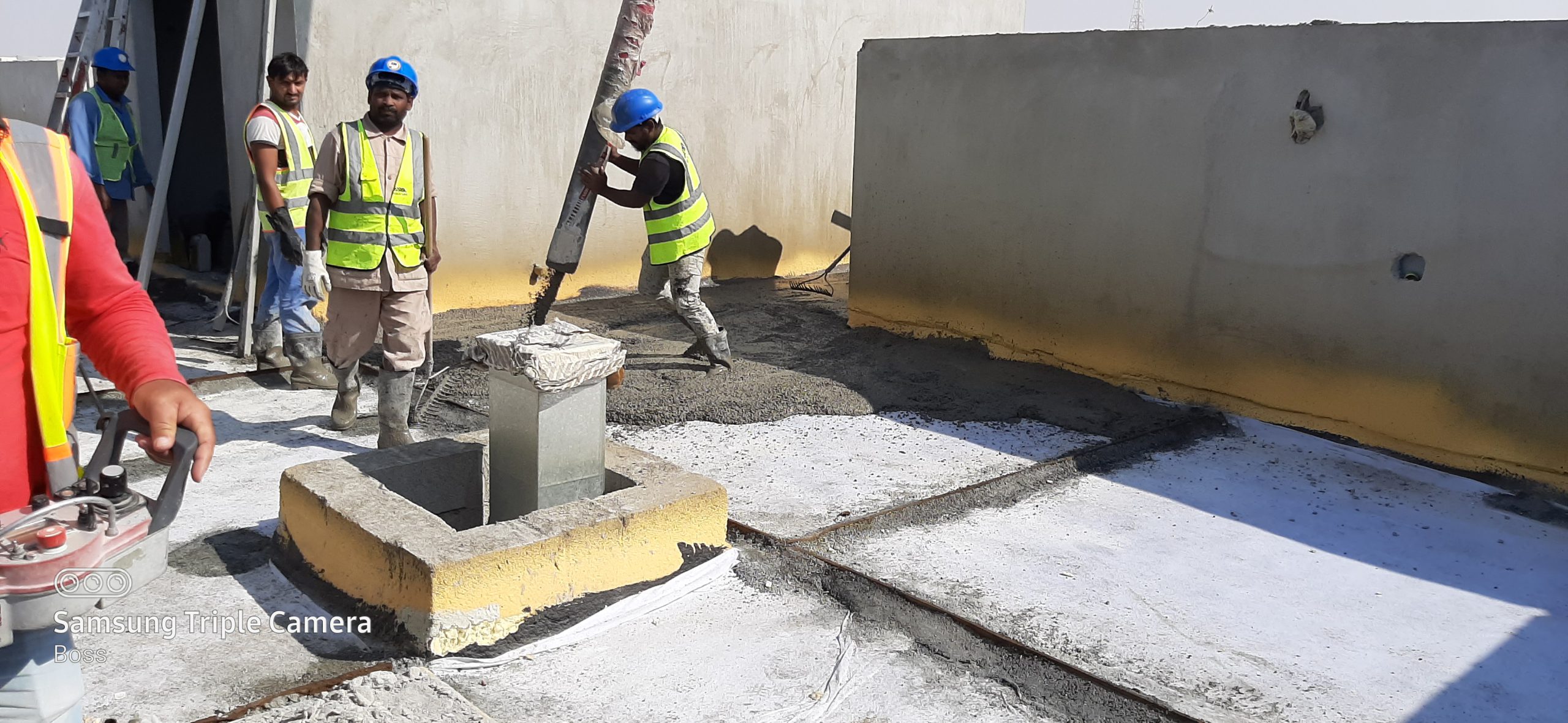
EXPANSION JOINT TREATMENT
Once the screed is completely cured, all of the joints created by the flexcell board will be opened and threatened with ACT sealant with 20 mm diameter backing rod for accommodating the movement of the concrete
APPLICATION OF SEALANT
- Prepare angle fillet (100x100mm) all around parapet skirting and concrete foundations. k. After the treatment of the joints and completion and curing of the applied angle fillet, and the casted screed, saturate concrete surface with clean water.
- While the surface is still visibly damp (but free of standing water), using brush or roller, a two coats of ACRYLIC WATER PROOFING COATING TWO COATS will be applied above the screed. The applied final coat will be allowed to full cure for 7 days before allowing any traffic on the roof.
TOP COAT FINISHING
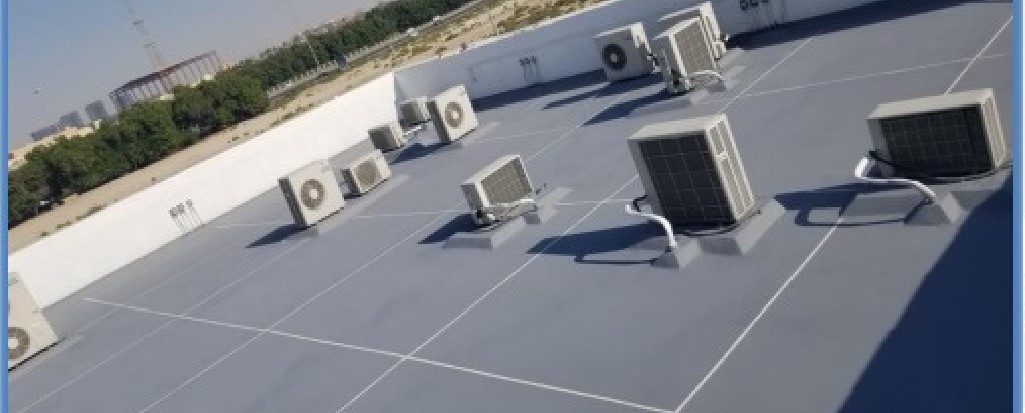